New Exploration ROBOTECH Helps Beijing Benz Stamping Production Line Achieve Intelligent Advancemen
Company News | 2022-11-21 09:50 Page views:
Automotive stamping parts are indispensable in automobile manufacturing. In recent years, as the speed of automobile upgrades has accelerated, the level of automation and intelligence has continued to improve, and the scale of new energy vehicle production has continued to expand, its demand has continued to grow. At present, about 60%-70% of metal parts need to be stamped in the automobile manufacturing process. Therefore, automobile stamping parts are widely used in automobile manufacturing and can be used as in-car supports, structural reinforcements and parts on the body. Various covering parts and other parts.
Affected by the epidemic lockdown, the movement of people has been greatly restricted, which in turn has affected corporate production and logistics. The original lean production model of the supply chain has been affected. The JIT inventory management model of the modern automobile industry has also gradually changed. In order to solve the problem of inventory, production Pain points in business scenarios such as efficiency, planning and building unmanned/less-manned smart factories, and realizing digital transformation need to be solved urgently.
About BBAC
Beijing Benz Automobile Co., Ltd. (BBAC) is a joint venture between Beijing Automobile Co., Ltd., Mercedes-Benz Group Co., Ltd. and Daimler Greater China Investment Co., Ltd. It was formally established in 2005 and has an annual output of 100,000 vehicles. car production capacity.
As the demand for production capacity continues to increase, BBAC, which integrates research and development, engine and vehicle production, sales and after-sales services, has built a new generation of global benchmark new factory project in Beijing. It plans to realize the operation information of the entire factory through digital transformation. Interconnection and production capacity breakthroughs.
The new factory project covers stamping, welding, painting, final assembly and multiple auxiliary distribution lines. The large-scale application of automated and intelligent logistics equipment technology adopts a high-level three-dimensional automatic access system and a fully automatic 3D robotic arm. The production and manufacturing capabilities have achieved a significant breakthrough. . Among them, the fully servo stamping automatic line equipped in the stamping workshop completes the precise stamping of complex parts through digital stamping rhythm control, which greatly improves the strength and stability of body parts. The production cycle can reach 17 times per minute.
Build a three-dimensional warehouse for end pickers
As the first process of automobile production, stamping is the starting point of vehicle production and the beginning of automobile quality shaping. Its importance is self-evident.
As we all know, the end pick is a flexible tooling fixture and is an essential component in the stamping automation production line. In stamping production, various stamping parts are picked up by changing the end picker. When in use, the end picker is installed on the mechanical arm of the press, and the reciprocating motion of the mechanical arm and the vacuum suction cup on the end picker are used to pick up and place the stamping raw materials and process parts, thereby realizing the automation of handling. Functionally, it can be divided into two parts. There are 5 types of end pickers for stacking, loading, unloading and transitional turning. Each set of end picks is composed of these five end picks with different functions. Generally, one stamping part needs to correspond to a set of end picks.
In this digital factory with a modern structure, a total of 5 stamping production lines have been preset to produce large body parts for models that are about to be put into production. There are thousands of sets of matching end pickers. In order to achieve intelligent production management, improve production efficiency and enhance the workshop's caching capacity, Weiben Electromechanical planned an overall logistics solution in the factory for it, and ROBOTECHH built it. An automatic storage system for the three-dimensional warehouse of stamping line end pickers has been installed.
ROBOTECH fully interprets the space-saving and highly intelligent advantages of smart logistics systems and created a 2-lane smart pallet three-dimensional warehouse in an 11-meter-high warehouse space, containing a total of about 200 storage spaces, fundamentally solving the BBAC stamping production line There are many types and large quantities of end picks for warehousing needs, and it can save space while being highly connected to the stamping production line to meet the storage and replacement of end pick tools, and achieve an increase in production capacity in a limited workshop area.
Since the pallet carrier of this project is an end picker turnover trolley, it faces huge challenges in terms of smoothness and accuracy in entering and exiting the warehouse. In order to prevent the end picker from slipping from the carrier, ROBOTECHH added two 270mm high pad beams at each storage compartment end of the beam-type shelf to prevent the wheels of the trolley from touching the ground, ensuring the stability of the end picker turnover trolley. And an anti-skid device is added to the cargo platform to effectively improve the overall stability and safety factor.
Schematic diagram of end picker trolley Specifications: L1200*W2500*H1600mm
The requirements of modern automobile industry production have also promoted the continuous development of stamping processes towards flexibility and automation, and the construction of the auto parts supply chain logistics system has been continuously strengthened in terms of inbound logistics, in-factory logistics and after-sales spare parts logistics. In the future, ROBOTECHH will continue to help companies realize the intelligent transformation of factory logistics, and meet the customized market needs of customers while ensuring production rhythm and quality.
New Exploration ROBOTECH Helps Beijing Benz Stamping Production Line Achieve Intelligent Advancemen
- Categories:Company News
- Author:
- Origin:
- Time of issue:2022-11-21 09:50
- Views:
(Summary description)
New Exploration ROBOTECH Helps Beijing Benz Stamping Production Line Achieve Intelligent Advancemen
(Summary description)
- Categories:Company News
- Author:
- Origin:
- Time of issue:2022-11-21 09:50
- Views:
Automotive stamping parts are indispensable in automobile manufacturing. In recent years, as the speed of automobile upgrades has accelerated, the level of automation and intelligence has continued to improve, and the scale of new energy vehicle production has continued to expand, its demand has continued to grow. At present, about 60%-70% of metal parts need to be stamped in the automobile manufacturing process. Therefore, automobile stamping parts are widely used in automobile manufacturing and can be used as in-car supports, structural reinforcements and parts on the body. Various covering parts and other parts.
Affected by the epidemic lockdown, the movement of people has been greatly restricted, which in turn has affected corporate production and logistics. The original lean production model of the supply chain has been affected. The JIT inventory management model of the modern automobile industry has also gradually changed. In order to solve the problem of inventory, production Pain points in business scenarios such as efficiency, planning and building unmanned/less-manned smart factories, and realizing digital transformation need to be solved urgently.
About BBAC
Beijing Benz Automobile Co., Ltd. (BBAC) is a joint venture between Beijing Automobile Co., Ltd., Mercedes-Benz Group Co., Ltd. and Daimler Greater China Investment Co., Ltd. It was formally established in 2005 and has an annual output of 100,000 vehicles. car production capacity.
As the demand for production capacity continues to increase, BBAC, which integrates research and development, engine and vehicle production, sales and after-sales services, has built a new generation of global benchmark new factory project in Beijing. It plans to realize the operation information of the entire factory through digital transformation. Interconnection and production capacity breakthroughs.
The new factory project covers stamping, welding, painting, final assembly and multiple auxiliary distribution lines. The large-scale application of automated and intelligent logistics equipment technology adopts a high-level three-dimensional automatic access system and a fully automatic 3D robotic arm. The production and manufacturing capabilities have achieved a significant breakthrough. . Among them, the fully servo stamping automatic line equipped in the stamping workshop completes the precise stamping of complex parts through digital stamping rhythm control, which greatly improves the strength and stability of body parts. The production cycle can reach 17 times per minute.
Build a three-dimensional warehouse for end pickers
As the first process of automobile production, stamping is the starting point of vehicle production and the beginning of automobile quality shaping. Its importance is self-evident.
As we all know, the end pick is a flexible tooling fixture and is an essential component in the stamping automation production line. In stamping production, various stamping parts are picked up by changing the end picker. When in use, the end picker is installed on the mechanical arm of the press, and the reciprocating motion of the mechanical arm and the vacuum suction cup on the end picker are used to pick up and place the stamping raw materials and process parts, thereby realizing the automation of handling. Functionally, it can be divided into two parts. There are 5 types of end pickers for stacking, loading, unloading and transitional turning. Each set of end picks is composed of these five end picks with different functions. Generally, one stamping part needs to correspond to a set of end picks.
In this digital factory with a modern structure, a total of 5 stamping production lines have been preset to produce large body parts for models that are about to be put into production. There are thousands of sets of matching end pickers. In order to achieve intelligent production management, improve production efficiency and enhance the workshop's caching capacity, Weiben Electromechanical planned an overall logistics solution in the factory for it, and ROBOTECHH built it. An automatic storage system for the three-dimensional warehouse of stamping line end pickers has been installed.
ROBOTECH fully interprets the space-saving and highly intelligent advantages of smart logistics systems and created a 2-lane smart pallet three-dimensional warehouse in an 11-meter-high warehouse space, containing a total of about 200 storage spaces, fundamentally solving the BBAC stamping production line There are many types and large quantities of end picks for warehousing needs, and it can save space while being highly connected to the stamping production line to meet the storage and replacement of end pick tools, and achieve an increase in production capacity in a limited workshop area.
Since the pallet carrier of this project is an end picker turnover trolley, it faces huge challenges in terms of smoothness and accuracy in entering and exiting the warehouse. In order to prevent the end picker from slipping from the carrier, ROBOTECHH added two 270mm high pad beams at each storage compartment end of the beam-type shelf to prevent the wheels of the trolley from touching the ground, ensuring the stability of the end picker turnover trolley. And an anti-skid device is added to the cargo platform to effectively improve the overall stability and safety factor.
Schematic diagram of end picker trolley Specifications: L1200*W2500*H1600mm
The requirements of modern automobile industry production have also promoted the continuous development of stamping processes towards flexibility and automation, and the construction of the auto parts supply chain logistics system has been continuously strengthened in terms of inbound logistics, in-factory logistics and after-sales spare parts logistics. In the future, ROBOTECHH will continue to help companies realize the intelligent transformation of factory logistics, and meet the customized market needs of customers while ensuring production rhythm and quality.
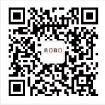