Smart Manufacturing Upgrade, Leading the Future of Printing | ROBOtech Helps Suzhou Mycolor Launch the Industry's First Integrated Warehouse Logistics and Production Process Project
2025-07-23 10:34
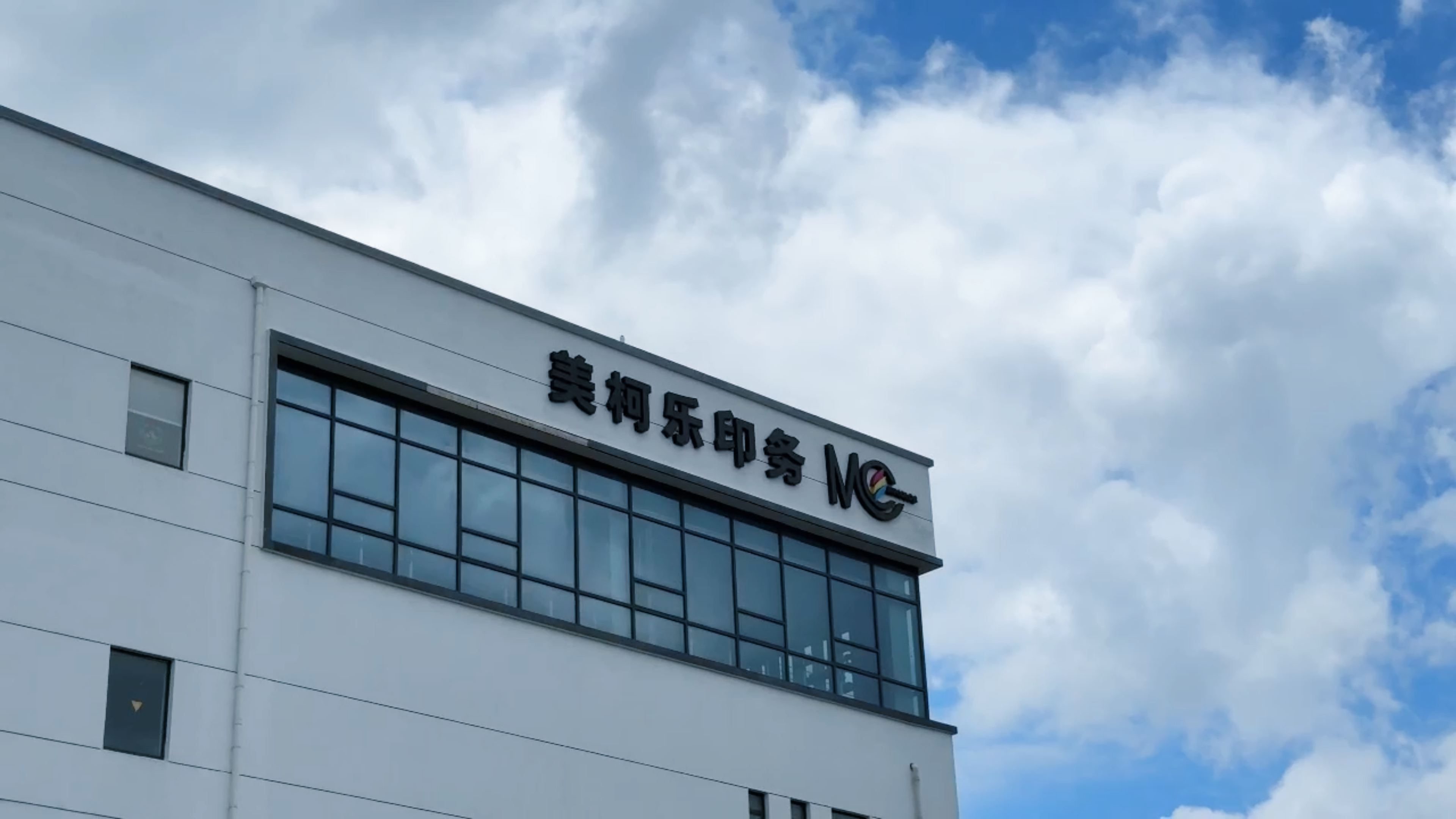
In today's increasingly competitive printing and packaging industry, efficient and precise warehouse logistics management has become the key for enterprises to improve quality and efficiency.
Warehouse Dilemma of Industry Leaders
Suzhou Industrial Park Mycolor Plate Making & Printing Co., Ltd. (referred to as "Mycolor"), founded in 1998, is a modern high-tech comprehensive printing enterprise. It serves well-known enterprises such as Jinguang and Goodbaby, as well as more than 20 publishing units including Beijing People's Education Press. It is also the designated bill printer for Jiangsu Provincial Department of
Finance and Local Taxation Bureau, with remarkable strength.
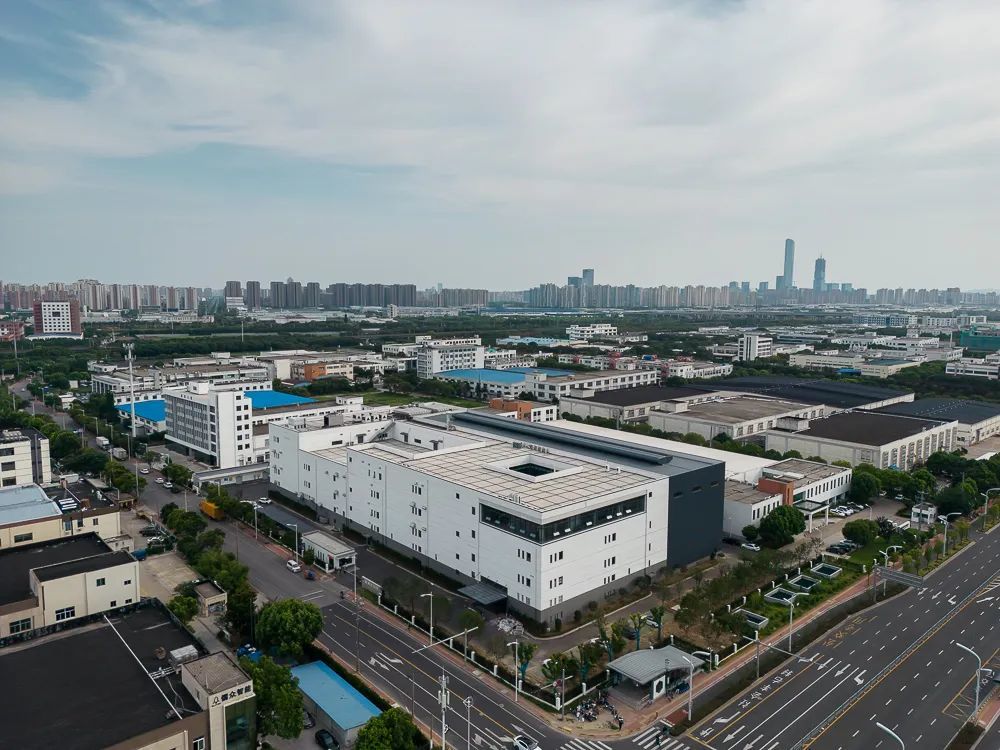
However, with rapid development, Mycolor's traditional warehousing model has gradually revealed bottlenecks. The traditional floor-laying warehousing has prominent problems such as difficulty in finding goods, difficulty in moving goods, low space utilization and low management efficiency. Moreover, due to the disconnection with the production line, the transportation volume of each link on site is huge, which affects the production progress and operational efficiency.
To break the shackles, Suzhou Mycolor turned its attention to the field of intelligent warehousing, and finally chose to cooperate with ROBOtech, which has rich experience and advanced technology in this field, to jointly build a green printing smart factory.
ROBOtech's Customized Solutions - Full Coverage from Technology to Equipment
In response to Suzhou Mycolor's warehousing pain points and production needs, ROBOtech provided a customized solution covering system design, equipment supply and full-process services, realizing seamless connection between warehousing and production.
Intelligent Hardware Builds a Solid Foundation
Storage equipment: Including vertical warehouse shelves and line-side warehouse shelves. The vertical warehouse area is 21 meters high with 8318 cargo positions; the second and third floors are equipped with line-side warehouses containing 416 goods, each carrying 2000kg, to meet the storage needs of materials in different production stages.
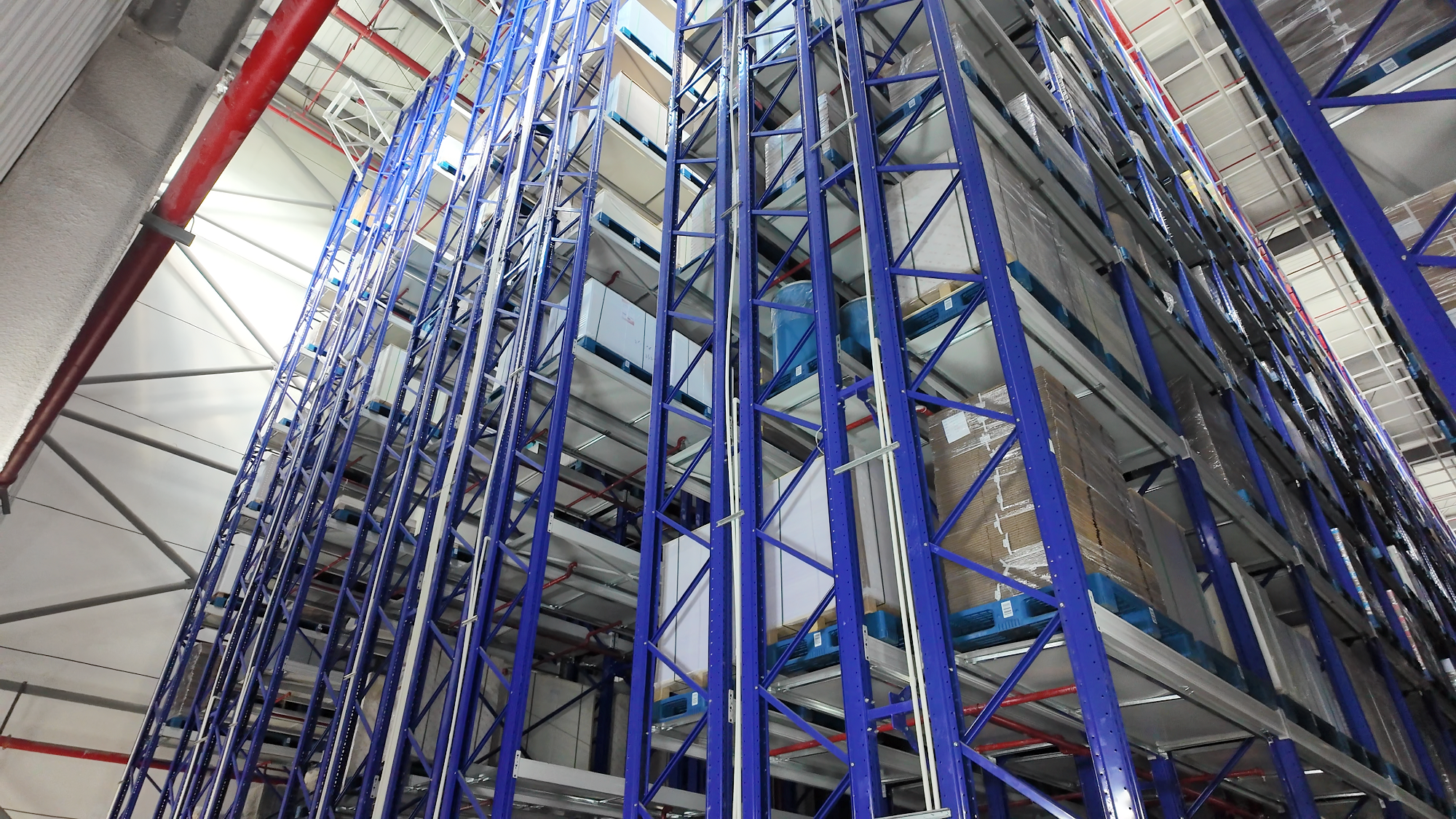
Handling equipment: 1 single-deep stacker and 3 double-deep stackers are responsible for the precise access of materials in the three-dimensional warehouse; conveying equipment such as conveyors, elevators, pallet shuttle RGVs, and AGVs build cross-regional material transportation channels, realizing the automatic circulation of materials between floors and production links.
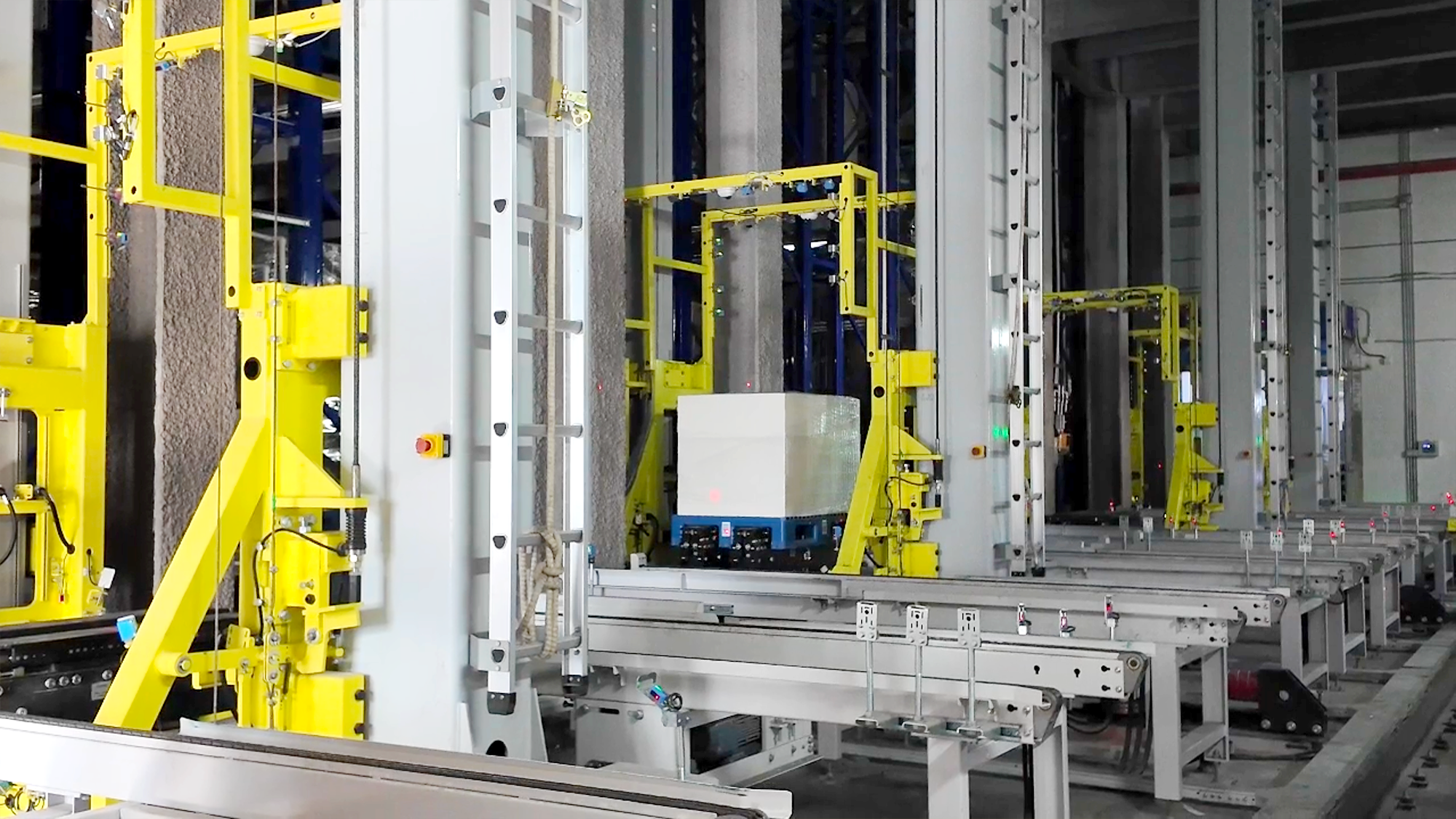
Software Brain Drives Intelligent Operation
Warehouse Management Software (WMS) and Warehouse Control System (WCS) are adopted to realize intelligent management and precise control of warehousing operations. Through interface technology, they are connected with Mycolor's MIS system to the information flow and realize data intercommunication.
Innovative Design Addresses Pain Points
1.Customized ultra-low conveyor line: directly connected with Mycolor's production equipment to realize "non-stop feeding", avoiding production interruption due to material supply, and greatly improving production continuity.
2.Flexible fork design: taking into account the handling needs of large and small materials, flexibly adapting to the diverse material specifications in the printing industry, and improving equipment utilization.
3.Flexible cargo position design: adopting the form of mixed placement of large and small pallets, each cargo position can place three small pallets / two medium pallets / one large pallet, greatly improving the utilization rate of the vertical warehouse.
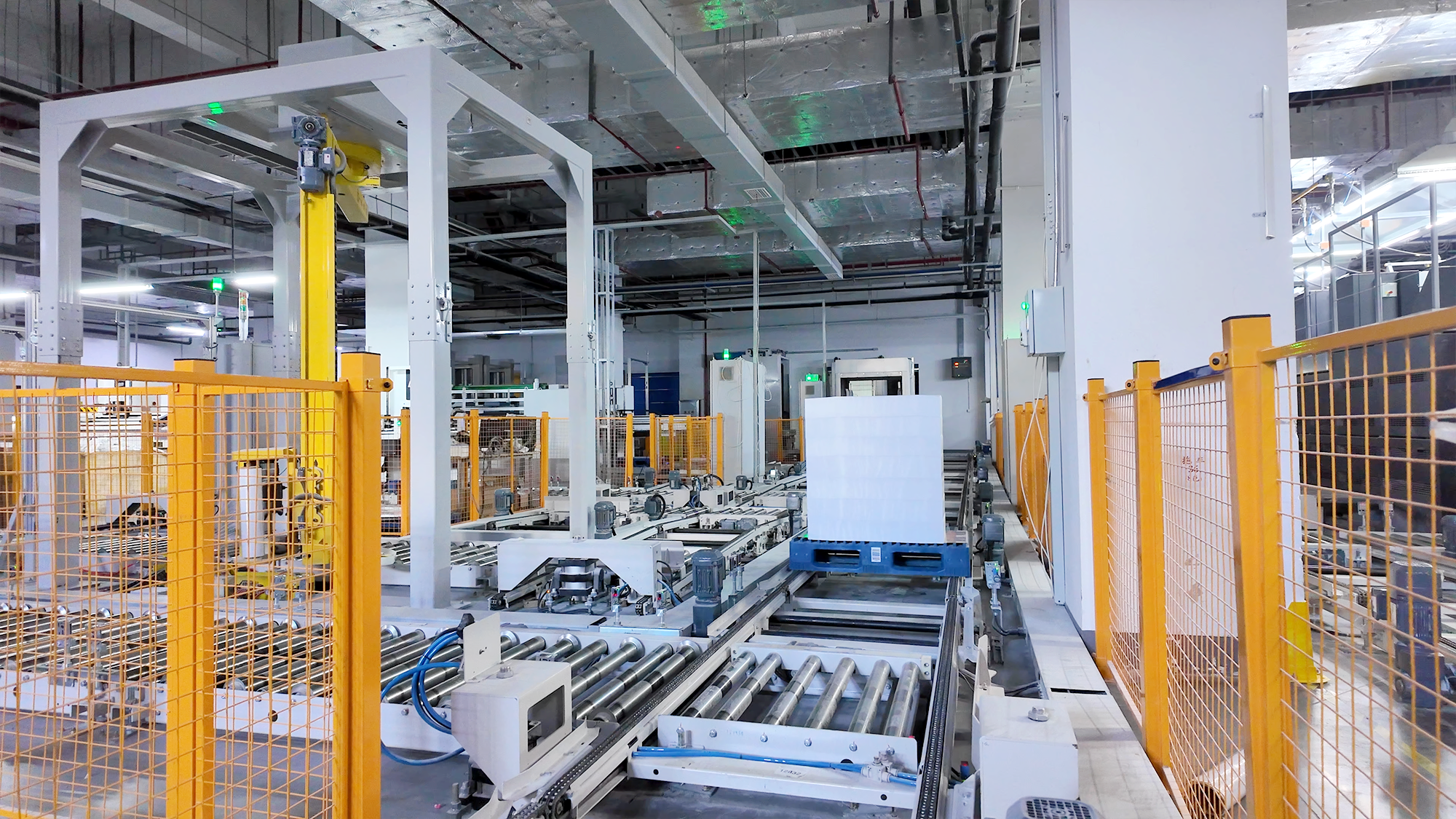
Implementation Effect - Double Leap in Efficiency and Quality
The implementation of ROBOtech's intelligent warehousing system has brought all-round operational improvements to Mycolor:
Intelligent management: The application rate of intelligent equipment and information software exceeds 70%. The equipment status is monitored in real time, the production tasks are visualized and dispatched, and the operation plans are automatically generated, data collected and dispatched.
Precise logistics: Automatic identification technology is applied to realize precise positioning and full tracking of materials. Workshop logistics realizes automatic selection, distribution and transportation, greatly reducing manual intervention and errors.
Quality traceability: Key processes are equipped with intelligent testing equipment, and quality information is automatically entered into the system to realize effective traceability of product quality.
Improvement of environment and safety: A workshop environment intelligent monitoring and adjustment system is deployed, and complete safety protection measures are equipped to improve the overall working environment safety level.
ROBOtech's intelligent warehousing system built for Mycolor has outstanding performance in the application of intelligent equipment, production scheduling, and integration of logistics and warehousing, accurately matching the production characteristics of printing enterprises, enhancing Mycolor's core competitiveness in the fierce market competition, and laying a solid foundation for sustainable and high-quality development.
In the future, ROBOtech will continue to deepen in the field of intelligent warehousing, and help more industry enterprises break through development bottlenecks and realize intelligent upgrading with advanced technology and customized solutions.